English
Watanabes: A New Generation of Indigo Dyers Keeping the Tradition Fresh
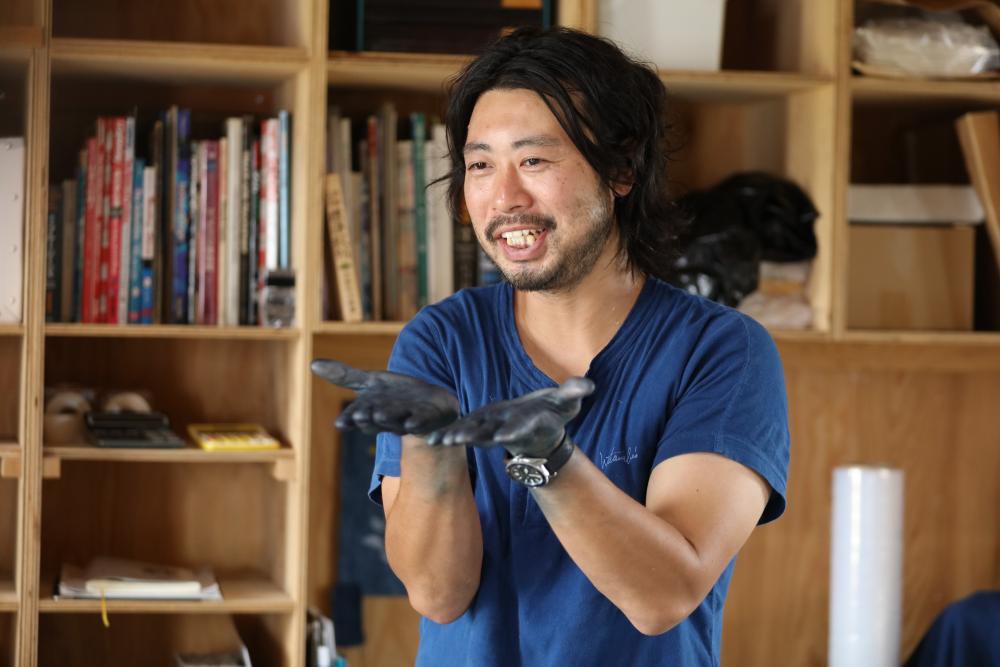
When you enter the small wooden studio of Watanabes in Tokushima’s Kamitaita-cho area, there are three things that stand out: the strong smell of fermenting indigo leaves, the young fresh faces of the staff (all sporting super stylish indigo-dyed cotton masks), and the blue hands of owner Kenta Watanabe.
“Are your hands always blue?” I ask him. He nods, laughing, and reveals he’ll be visiting an onsen later to properly scrub the dye off.
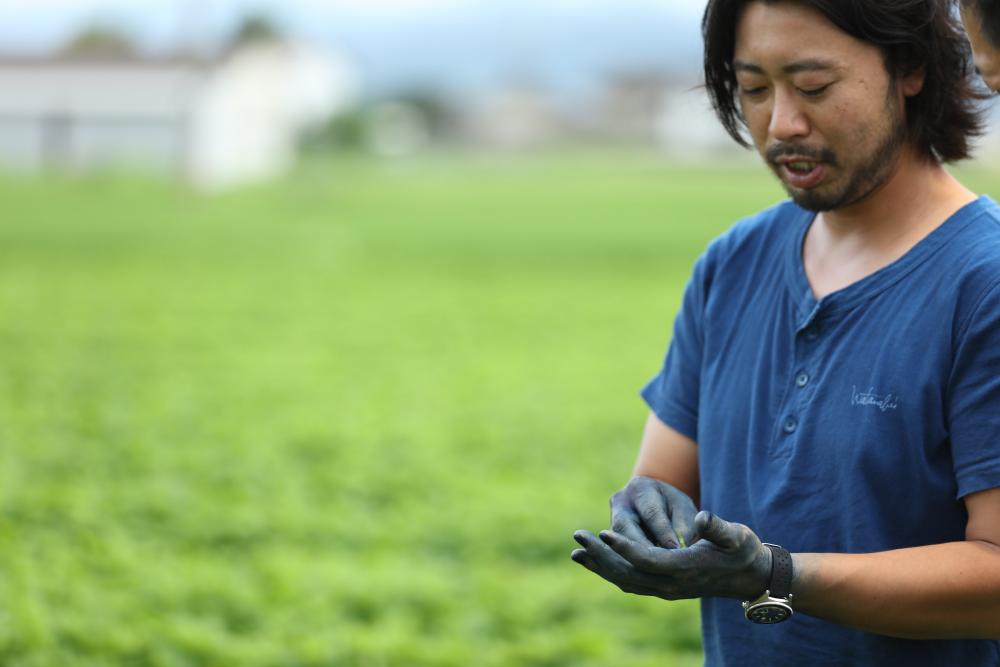
Kenta Watanabe, the owner of Watanabes, started his company in early 2019. His long hair, warm smile and youthful demeanor immediately convey the message that he’s not your ordinary, traditional dyer. And that’s before you’ve even heard the full story.
After building up experience at another company, he decided he wanted to break with tradition and embrace sixth sector industry – meaning growing the indigo plants, processing the dye, dyeing and designing garments, and selling.
Watanabes does it all.
Why is this unusual? Because in traditional indigo farming, different people concentrate on only one area and see farming and dyeing as two separate things. He came up against some resistance, but has persevered and is gradually finding his own place not only in the local but also in the overseas market. The company even sells their dye to one artist in Amsterdam.
Combining all production tasks into one company means visitors can learn about the entire process too, from start to finish. You can walk around the area surrounding the studio and pass by a Kintoki pig pen who happily feed on sweet potato and whose feces are used to fertilize the indigo plant field, which is just across the road.
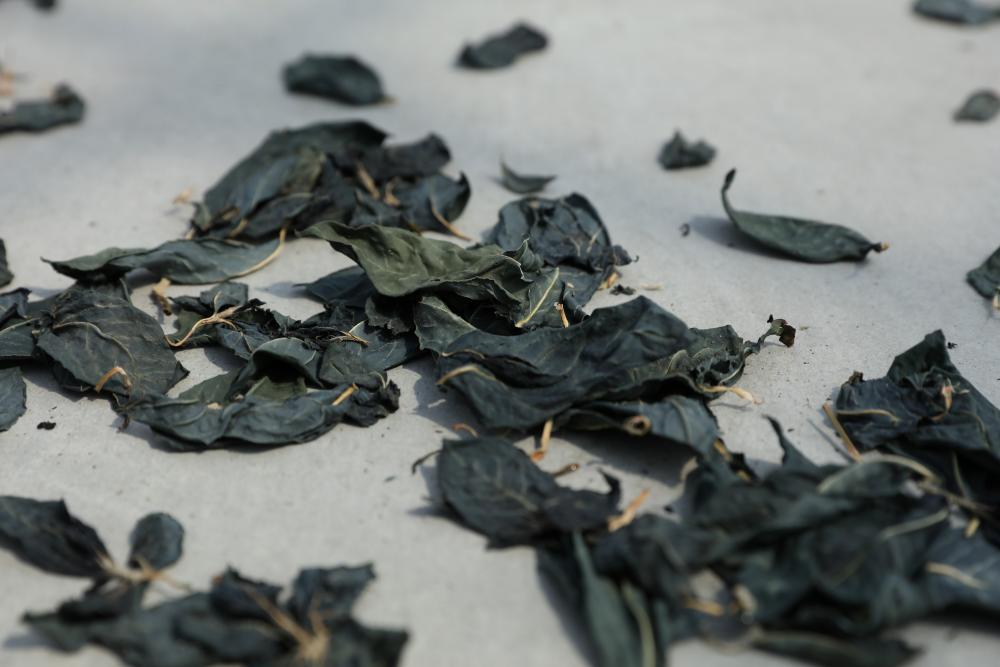
You can then cross back to the other side of the studio and enter a type of greenhouse where the harvested leaves dry out, their color transforming from green to the inky color for which they’re famous (in case you’re wondering, as I was, the dried leaves can be enjoyed in hot water, should you be inclined to enjoy a cup of indigo tea).
After that, you can visit the custom-built shed in which the dried leaves are stored before they’re transferred into troughs of water in the studio to ferment. Only four ingredients are used in the fermentation process: the fermented leaves (sukumo), wood ash, shell ash and wheatbran, making this an entirely chemical-free process.
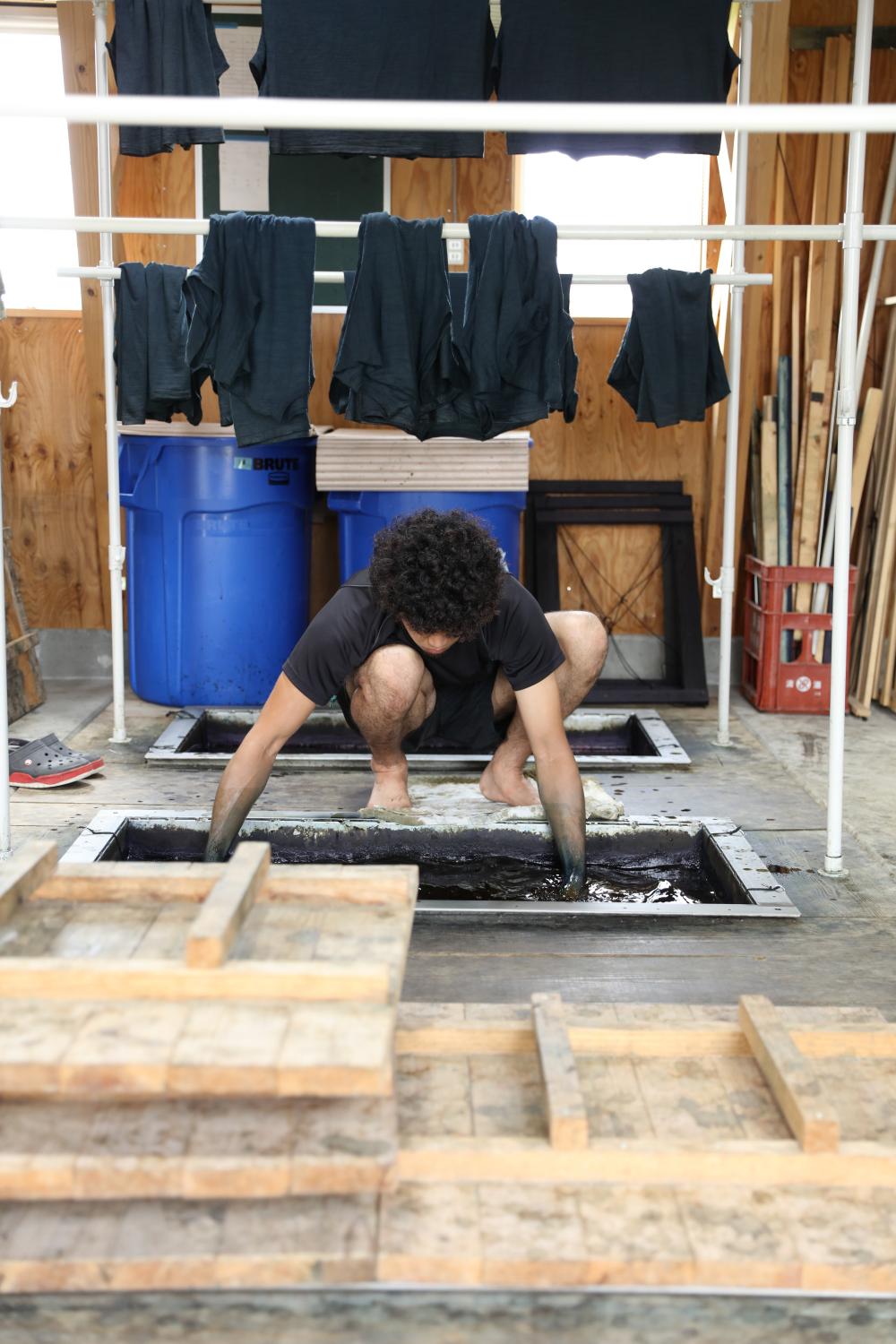
It’s here, in the studio, where you can enjoy trying a spot of indigo dyeing yourself. Wearing disposable gloves, we dipped a piece of white cotton fabric into the deep blue water, swishing it around, squeezing out air bubbles, and making sure the dye was evenly distributed.
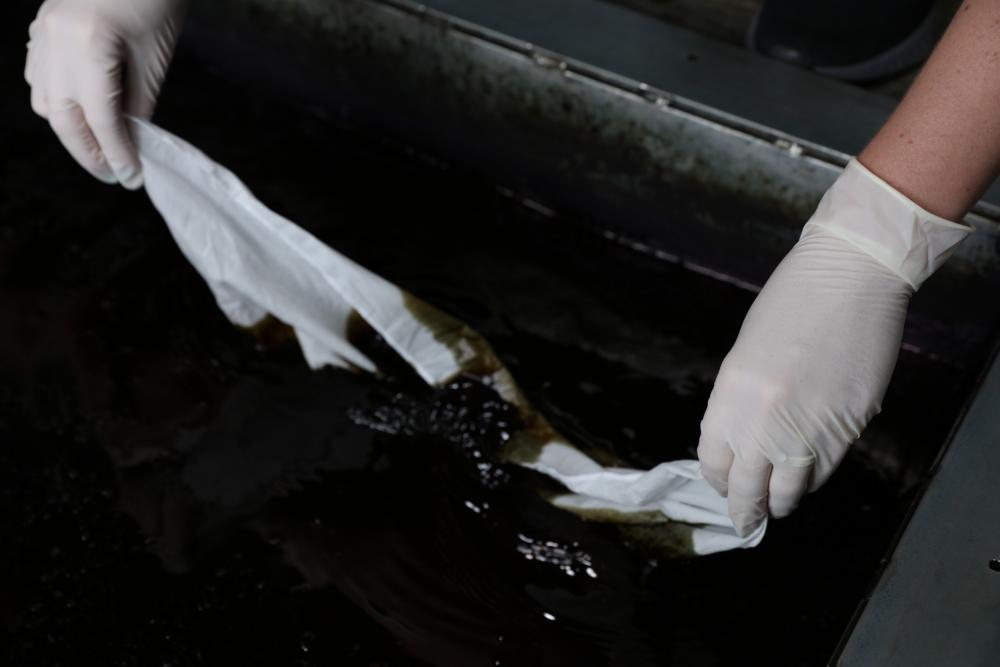
We then rinsed and hung the fabric up to dry. Watanabe and his staff explained how they might dip the fabric in more or fewer times depending on how deep they wish the end color to be.
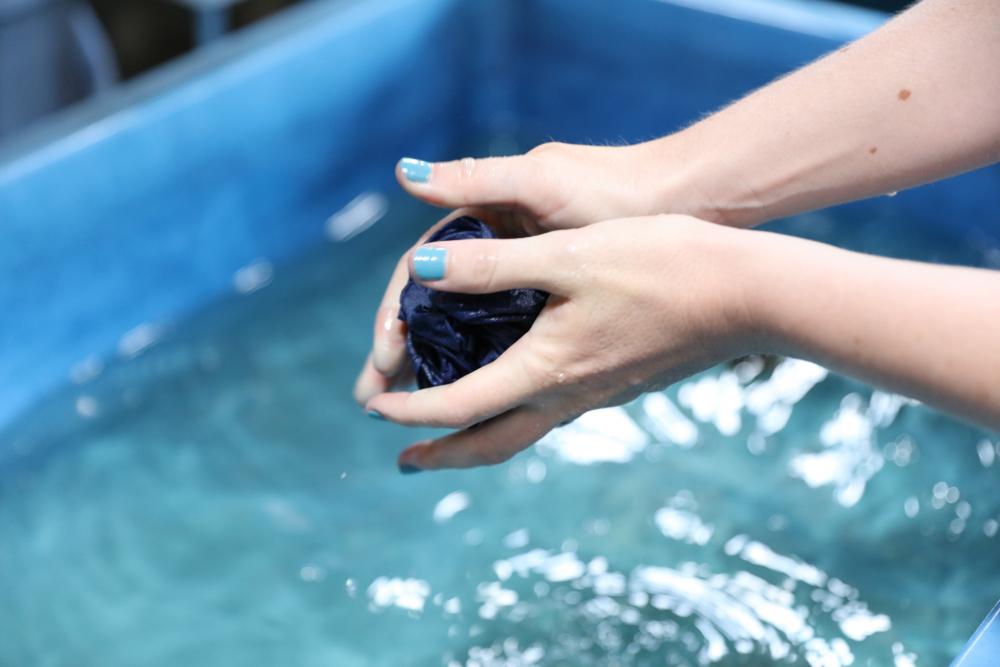
Every item – such as the dyed aprons hanging up along one wall waiting to be collected by a client – is hand-dyed, giving it a personal, unique touch.
Lately, the staff tell us, they’ve seen an increase in conscious shoppers stopping by for a visit. This is a good sign, because it means not only is the art of indigo dyeing becoming more associated with sustainability, but its popularity is receiving a fresh bout of interest from younger clientele who up until recently might have viewed indigo dyed products as a tad old fashioned.
Watanbes aims to reach even more people in the future by traveling to Tokyo to hold workshops and also encouraging people to visit them at the studio.
Wondering what to bring along for your own dyeing experience? Watanabes recommends using one of your own items to reinvigorate and extends its life: “Perhaps even your wedding dress!”
Watanabe’s
Where: 314-10, Sebe, Kamiita, Itano, Tokushima Prefecture
More info: https://www.watanabezu.com